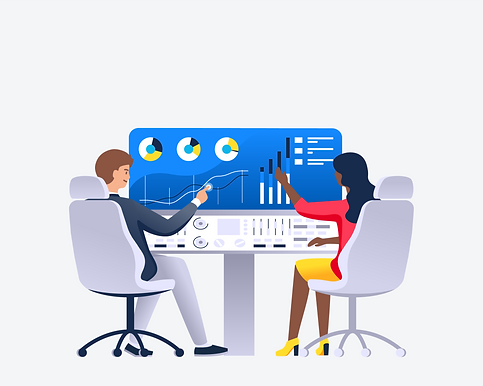
1C:ERP for India
ERP for Enterprises
All-in-One ERP solution for automation of business processes in Medium and Large Enterprises.
1C:ERP is powered with 1C:Enterprise
Procurement
-
Manage inventory stock balance and production demand
-
Automatically generate POs upon min/max stock settings and production/sales demands statistics including shipping leg

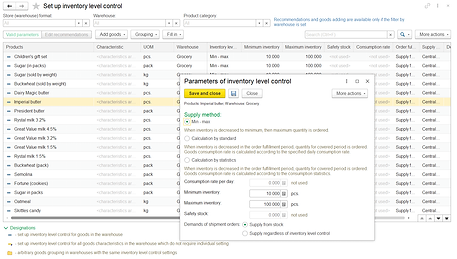
Warehouse and Inventory
-
Create and manage graded warehouse structure, storage bins
-
Manage multiple warehouses
-
Use batches, series, expiration dated for Your inventory
-
Control Your stock level using multiple methods
-
Use delivery tools
Production Management
-
Enjoy visual presentation of the product’s structure
-
Use resource specifications
-
Two level production plan: main and local dispatcher
-
Use operational, interval and “Drum-Buffer-Rope” scheduling
-
Plan “bottleneck” production areas
-
Manage priorities (VIP orders)
-
Calculate time needed for transportation of inventory and in-process queue
-
Forecast the whole process
-
Dispatch production on inter-workshop and intra-workshop levels

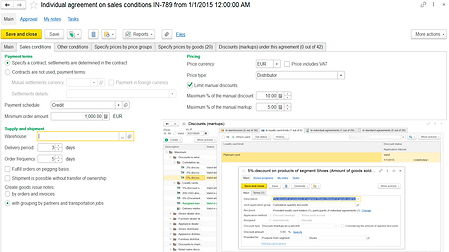
Sales Management
-
Manage customer orders subject to standard and individual agreements on sales conditions
-
Organize clients’ self-service
-
Manage trade representatives
-
Monitor the condition of the sales processes
-
Configure price-lists with inventory information
-
Use various pricing and discounts based on different conditions
-
Monitor sales processes using sales pipeline and sales funnel
-
Use sales planning and forecasts
-
Create sales reports by company/client/product/department/employee
CRM and Marketing
-
Track interactions with customers
-
Use business-process road maps to automate business-processes
-
Maintain customers' loyalty with rewards, membership cards, flexible discount system
-
Use BCG Matrix
-
Perform ABC/XYZ analysis
-
Use grievance redressal mechanism
-
Evaluate employees' performance
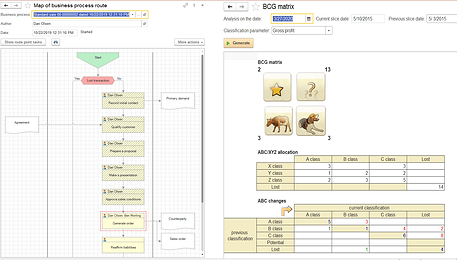
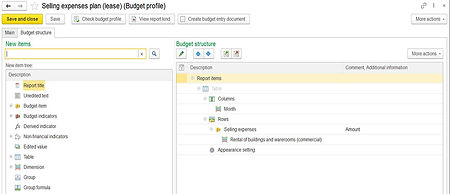
Budgeting
-
Manage your budgets using extra parameters
-
Draft Your budgeting scenarios
-
Forecast Your financial indicators
-
Perform targets and goals achievement analysis
Net Cost Calculation and Financial Result
-
Classify resources used in production
-
Allocate costs to different activities
-
Count expenses in terms of cost and quantity
-
Separate cost by orders
-
Perform quantity resource accounting for unfinished production
-
Use different methods to distribute expenses (manufacturing costs/spheres of activities/future expences)
-
Configure reports for financial results analysis


Maintenance And Repair
-
Plan maintenance of Your machinery to minimise downtime
-
Plan repairs and control repair orders from machinery operators
-
Keep track of equipment output volume
Payroll & HR Management
-
Plan the demand for personnel
-
Manage employees' motivation
-
Organise personnel documentation: employment, vacations, staff movements, dismissals
-
Use various payroll schedules
-
Calculate remuneration in accordance with employees' effectiveness
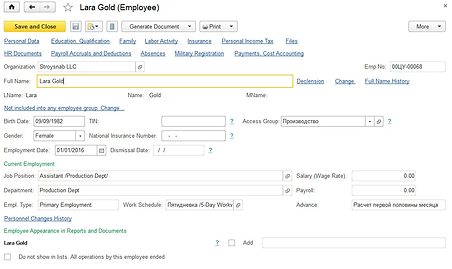